.
,
, ,
.
.
.
, .
15-20% , 180, 45-55% ,
300-350.
, (82-87%),
(11-14%), (0,1-7%), (0,001-1,8%), (0,5-1%).
30-50%, 25
75%. , ,
(10-20%).
.
, .
, , , ,
, .
-
,
.
, , ,
8% 2020 . 20-25%.
.
( , ,
) (, ,
.)
,
, .
,
100%.
, , .
.
.
,
() .
. ,
.
: , ,
, ,
.
,
.
.
,
,
. ,
, .
() ,
- () .
, 1
, 170-175
(1).
350
(2), .
. ,
, ;
.
,
. ,
, ..
, .
. , 300-350 ,
200-300
, 160-200
. ,
(3) (4).
(2).
,
(6), .
.
(5),
400-420.
(6), 5,3-8,0 .
.
.
, ;
, ,
. , ,
.
. , ,
.
.
.
:
1.
- ;
2.
, , ,
.
(480-530),
(2-4 ), .
,
( 80% 2)
.
,
, :
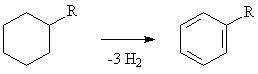
()
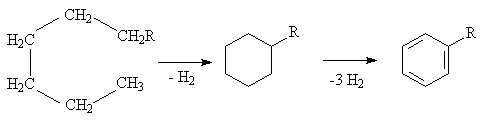
,

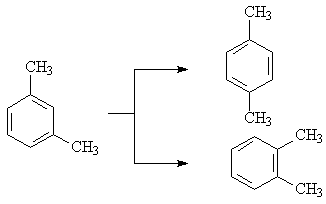
, .
530 217 /,
254 /.
.
, ,
.
,
.
.
, .
.
480 530.
, . ,
.
2-4
2 : .
.
,
, .
2 :
,
. 2 : ,
6:1 10:1.
. ,
. 1 .
.
, :
, , , , .
,
; , , . ,
, ,
, .
,
. 0,3-0,65%.
6 1 ,
,
. ,
.
.
.
.
2.
(5),
(6) ,
. (4) ,
. (4)
(5) ( )
(2). (1) 2
H2S
3 . (10)
, (10) (6).
(7),
(8) (9) .
(7) (8) (6). (9) .
(10)
, ,
(11).
(13)
. ( ) (13) .
(12)
, ,
,
.
(C4H10, C3H8 C2H6),
. (13) (17) (14). ,
(15)
(16).
,
. (14)
(17)
.